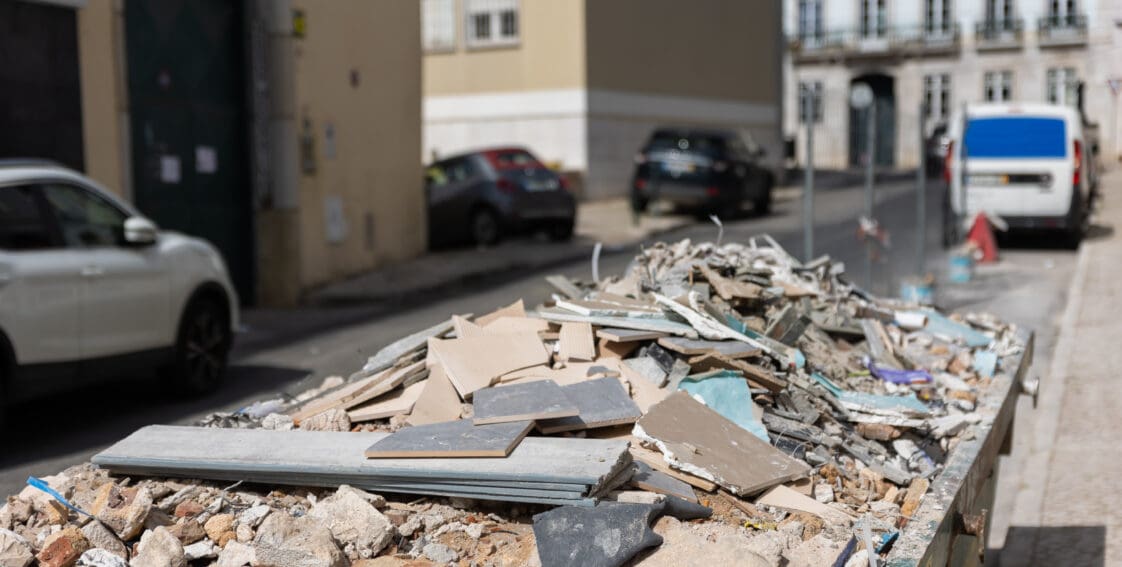
Understanding the Different Types of Waste & How to Manage Them
In the past, manufacturing companies were responsible for producing tons of waste. In fact, the EPA reported in the 1990s that manufacturers contributed to 265 million tons of waste. To combat this, manufacturers have begun to manage waste through recycling, treatment, and energy recovery efforts.
In this article, we’ll describe the three major types of waste manufacturers produce and highlight the most effective industrial waste processing solutions for each type.
Types of Industrial Waste
Any solid, liquid, or gaseous residual matter stemming from industrial activity qualifies as industrial waste. Although industrial waste can be classified as hazardous or non-hazardous, both classes can cause significant damage to the environment. Waste can generally be categorized into three types: solid, toxic, and chemical.
Solid Waste
Solid waste includes scrap metals, plastic, wood, paper, packaging material, and cardboard, and can be generated by manufacturing processes like:
- Pharmaceutical
- Food and beverage
- Consumer packaged goods
Depending on the nature of these materials, industries can recycle them to help minimize waste and resources.
Toxic Waste
Toxic waste is a subset of hazardous waste and is usually a byproduct of other materials generated from applications like chemical manufacturing, metal processing, and petroleum refining.
Toxic waste can be in solid, liquid, or gaseous forms and typically contains harmful chemicals, heavy metals, or other dangerous substances that can be detrimental to humans, animals, and plants if not properly disposed of.
The characteristics of toxic waste include toxicity, corrosivity, reactivity, ignitability, and persistence.
Chemical Waste
Chemical waste is any waste material that contains harmful chemicals. Compared to toxic waste, it’s a broader category that includes all waste containing chemicals, whether hazardous or non-hazardous. This type of waste is usually generated from industrial, laboratory, or household activities.
Managing Industrial Waste
Shredders
The first step in managing all three types of waste is incorporating a shredder, which helps reduce the size of waste materials and makes it easier and more cost-effective to handle and transport them for further processing. Please visit our Industrial Shredder guide for more insight into how they work and their different designs.
As a broad definition, shredders break down large items into smaller pieces and can be categorized as single-shaft, dual-shaft, and quad-shaft.
Compaction
For certain solid wastes, balers or compactors compress waste materials to reduce their volume. Compactors are especially ideal for reducing the volume of general waste, such as organic waste, mixed recyclables, and non-recyclables.
Recycling & Recovery
Once the materials are broken down, they may be taken to a recycling facility for further processing.
Materials Recovery Facilities will sort and process recyclable materials, like paper, plastics, metal, and glass. Plastics may go through further mechanical recycling processes, like grinding, washing, and re-pelletizing) or chemical recycling to be converted into reusable materials. Metals are often recycled and recovered via shredding, magnetic separation, and smelting.
When dealing with non-toxic chemical waste, there are two primary recovery processes: solvent and material.
Thermal Treatment
Incinerators are often used to burn hazardous chemical waste and destroy harmful compounds. Pyrolysis and gasification processes may also be used to decompose organic waste material and produce syngas, oil, and char, which can be used as fuels or raw materials.
Chemical Treatment
Hazardous and non-hazardous chemical waste is often treated via neutralization or oxidation. The neutralization process involves adjusting the pH of acidic or alkaline waste to a neutral level, which makes it safer to dispose of or further process. Oxidation involves converting hazardous substances into less harmful compounds.
Biological Treatment
This method is reserved for organic waste. The two primary biological treatment methods are composting and anaerobic digestion. They are both similar processes, but they create different byproducts.
Composting involves the anaerobic decomposition of organic waste to produce nutrient-rich compost that’s used in agriculture and landscaping applications. Anaerobic digestion is where organic waste is broken down without oxygen to produce biogas (methane) and digestate. Biogas can be used as a renewable energy source, while digestate is a fertilizer.
Landfilling
This is the last step in the waste management process. If materials can’t be recycled, composted, or recovered/reused, they will be safely disposed of in an engineered or bioreactor landfill.
Our Shredder Recommendations
As mentioned earlier, shredding is often the first step in processing most waste.
Here are some of our recommended products:
Solid Waste—SHRED Series
JWC Environmental’s SHRED line is available in five models: 1-SHRED, 3-SHRED, 3-SHRED-2, 4-SHRED-2, and 7-SHRED-2. The 1-SHRED is recommended for lower-volume applications (43 ft3/hr), while the 7-SHRED-2 is our most powerful model with a throughput range between 891 and 1,504 ft3/hr.
These models can help you minimize transportation costs and improve digester/composter system efficiency. Each model features two rows of cutters that rotate slowly with high torque to shred tough materials and automated monitoring. Cutters can be configured based on your application and the materials you’re processing.
Toxic Waste—4-SHRED-2
The 4-SHRED-2 is designed to handle some of the most challenging solids and works exceptionally well for hazardous waste disposal. This shredder can handle both wet and dry waste (up to 393 ft3/hr) and can be configured for multi-stage grinding. The 4-SHRED-2 is also certified by the American Bureau of Shipping (ABS) and meets MARPOL Annex V regulations for marine applications.
It features all of the same benefits as the other SHRED models, but can be equipped with optional food-grade nickel-plated housing and stainless steel cutting chamber components. JWC Environmental also makes custom hoppers and stands for this model.
Chemical Waste—3- & 4-HYDRO In-line Grinder
Our 3-HYDRO and 4-HYDRO in-line grinders are specifically designed for chemical plants and oil/gas refineries and help protect downstream equipment like pumps, valves, and centrifuges.
Both grinders help precondition sludges, slurries, and waste materials to improve recovery. The 3-HYDRO has a flow rate of up to 2,450 GPM and comes with a standard 5-HP motor.
The 4-HYDRO is more powerful, with a flow rate of up to 6,860 GPM and a standard 10-HP motor. The 3-HYDRO and 4-HYDRO both feature dual-shafted cutter stacks that rotate slowly with high torque and a compact footprint, which makes them able to fit within most pipeline systems. Additionally, cutters can be configured with optional Wipes Ready® Cutter Technology for applications processing fibrous, sinewy, or stringy solids.
Have Questions? Contact JWC Environmental Today!
Founded in 1973, JWC Environmental is proud to be a trusted manufacturer of industrial waste processing equipment. We know that with industrial waste, there is no one-size-fits-all solution, so we work hard to find a solution that helps you overcome your unique challenges.
Please visit our blog for more industrial waste processing resources, or contact us today if you have questions about our shredders and grinders.