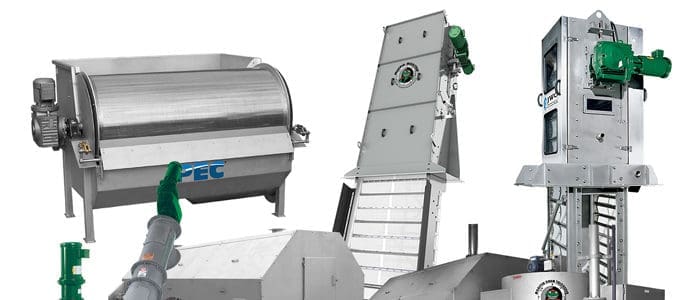
Guide to Wastewater Screening Equipment
Equipment Guide
- Types of Wastewater Screens
- Overview of Coarse Screening Solutions
- How to Select the Right Wastewater Screen
- Contact JWC Environmental Today
The main purpose of wastewater screening equipment is to remove solid materials from the wastewater system. Solid materials can contaminate waterways, damage equipment, and reduce the overall efficiency of the system, which is why they must be removed at all costs.
In this guide, we’ll cover the different types of wastewater screens available, and give you tips on how to select the right one for your plant.
Types of Wastewater Screens
Wastewater screens are primarily defined as either fine or coarse and can then be further split into other categories like rotary drum, band, auger, static, mechanical bar, and chain and rake.
Before discussing some of the specific subcategories, let’s first define the difference between fine and coarse screens.
Fine Screens
Fine screens help capture small amounts of plastic, hair, and paper and use self-cleaning mechanisms to prevent clogging. They are mainly used as a secondary treatment method.
Coarse Screens
Comparatively, coarse screens remove large non-biodegradable solids, including rags, wood, paper, and sanitary items. They are often used in the beginning stages of wastewater treatment, especially in settings when large debris is common.
Overview of Fine Screening Solutions
Fine screens can be split into several subcategories. In the following sections, we will cover each type of fine screening solution, how they work, how they’re used in the wastewater process, and highlight JWC Enviromental’s unique fine screening products.
Rotary Drum Screens
In the wastewater treatment process, rotary drum screens are used as a pre-treatment method to separate solids, including debris, grit, algae, and sludge, from liquids. When wastewater enters the drum, the waste passes through a screen mesh, which captures and retains the solids while the rest of the water flows through the screen.
There are two types of rotary drum screens: internally-fed and externally-fed. Internally-fed drum screens have an inlet located inside the drum, while externally-fed drum screens have inlets on the outside of the drum. Internally-fed drum screens are typically used when higher flow rates are needed, and externally-fed drum screens are generally used in plants with high oil or grease loadings and provide better overflow protection.
JWC Environmental offers internally-fed and externally-fed solutions: the Drumscreen Monster Internally Fed Rotary Screen and the Externally Fed Rotary Drum Screen.
The Drumscreen Monster is a fine screening solution designed for municipal applications with high flows (up to 12,000 gpm) and low solids. It’s engineered to provide membrane bioreactor (MBR) protection from fine particles and fibers and can be customized based on application requirements.
The Externally Fed Rotary Drum Screen is self-cleaning, designed for municipal applications with high oil, grease, and clarifier scum, and can handle flows up to 4,000 gpm. Like the Drumscreen Monster, it can be customized based on application requirements.
Band Screens
Band screens are a type of in-channel screening solution that typically consists of a series of panels or continuous belts that form a loop, rotating vertically between two sprockets. The rotating screen moves in a direction opposite to the flow of the water, so as the screen moves upward, it lifts the captured solids out of the water. Like other in-channel screens, band screens also have a self-cleaning mechanism to prevent clogging.
JWC Environmental’s band screen solution, the Bandscreen Monster®, consists of a center flow screen that captures small solids and hair. When wastewater enters the Bandscreen Monster, the center flow screen captures the solids while the water flows through the additional perforated screens. The perforated UHMW screening panels are designed to prevent hair pinning, which can cause clogs in the central flow screen.
Auger Screens
An auger screen is used to remove solid materials from a wastewater stream. Auger screens consist of two components: a transit tube and a spiral auger blade that runs inside the surface of the tube. The blade rotates slowly, pushing wastewater toward the outlet at the end of the tube. As wastewater flows through the screen, the blade catches solids and carries them toward the top of the transit tube. Once the solids reach the top of the tube, a scraper blade removes them and deposits them onto a collection hopper.
JWC’s compact, all-in-one Auger Monster™ removes all types of large solids, including grit, gravel, rags, clothing, and other debris, and is primarily used in high-solids facilities, including prisons. It’s easy to install, requires minimal maintenance, and integrates with our Muffin Monster® or Channel Monster® grinders to precondition solids entering the auger screen.
Static Screens
Static screens are often located in channels and tanks and consist of a flat or curved panel with closely spaced openings that trap solids while allowing water to pass through. As wastewater flows through the screen, solid materials (sticks, leaves, etc.) are caught in the slots. Eventually, the solid materials will build up on the screen’s surface, forming a mat or layer that filters finer particles. When the layer of solid material becomes thick enough, it is removed manually or automatically using a spray bar, scraper, or conveyor.
JWC’s cost-effective sidehill static screens are primarily used in static dewatering applications or in any wastewater treatment process where the solids can be more easily separated from liquids. Our sidehill static screens are available in the SHP and SHS models.
The SHP is a pressurized model with a high capture rate. It is commonly used for fiberglass, synthetic fiber, and starch recovery. It uses a fixed, curved, wedgewire screen and pressurized feed to capture and separate particles up to 0.006 inches. Designed for low-maintenance, the SHP features a pneumatic oscillating spray system that intermittently cleans the screen and a slot-feed design to prevent plugging.
The SHS is a simpler model with no motors or moving parts. It features a wedgewire screen with slots and uses gravity to capture and separate solids. Like the SHP, the SHS has a slot-feed design to prevent plugging by fibrous materials. It’s easy to install and is commonly used in meat processing, mineral, and forestry applications, including pen wash downs, coal washes, chip washing, and pulp thickening. The SHS does not feature a self-cleaning system and must be cleaned manually to ensure efficiency.
Overview of Coarse Screening Solutions
Compared to fine screening, there are only two types of coarse screening solutions: bar and chain and rake. In these next sections, we’ll discuss how each coarse screening solution works and highlight JWC Environmental’s innovative coarse screening products.
Mechanical Bar Screens
Mechanical bar screens help remove large particles from wastewater, including rags and plastic, and can be used as a primary pre-treatment method. Most mechanical bar screens feature vertically-mounted bars, which are responsible for capturing large solids. Mechanical bar screens also have self-cleaning capabilities.
JWC’s highly efficient Bar Screen Monster® is designed to remove large debris quickly and efficiently. Our heavy-duty but compact screen uses a reciprocating rake to clean the mechanical bar screen as it pulls out slugs of debris in headworks and pump stations. Our Bar Screen Monster is best suited for large storm flows.
Chain & Rake Screens
Stormwater treatment stations, headworks, and pump stations need a solution that can quickly remove heavy debris—that solution is a chain and rake screening system.
Chain and rake systems are typically installed in a stormwater collection basin or channel, where they can operate automatically or manually. The chain-driven rake moves along the length of the frame, dragging debris toward the collection point. Once the rake reaches the end of the frame, it lifts the debris out of the water and deposits it on a conveyor belt or collection system, where it is transported to a disposal area or recycling facility.
JWC’s Chain & Rake Monster® is an automated, heavy-duty bar screen rake specifically engineered to handle the most demanding water treatment needs. Our Chain & Rake Monster can remove large debris, including branches, leaves, and trash from stormwater; it’s also easy to maintain, as it features a pivot frame that can be easily accessed from the bottom of the screen.
How to Select the Right Wastewater Screen
Wastewater screening is the first line of defense during the filtration process. If your design fails to meet industry standards, you may end up damaging and clogging your equipment every week. That’s why it’s important to find the right screening equipment.
When selecting screens, the first area you should focus on is the wastewater itself. Find out which contaminants are in the wastewater. In many industrial operations, fats, oils, and grease are common. However, you should also consider other contaminants, like salt, surface-active agents, and corrosive matter. If you don’t identify and understand the contaminants in the wastewater, you may experience screen binding/clogging.
The flow rate is also crucial. How fast or slow will the wastewater move through the screen? For best efficiency, make your decision based on the maximum flow rate possible.
Finally, decide how important the byproducts are. Many industrial applications need to screen specific particles out of the effluent to re-use for another purpose. It can be a massive revenue generator for your company. Once you’ve chosen the target size of the particles, you can choose an appropriate screen.
Contact JWC Environmental Today
Still have questions? JWC Environmental is here to help! We’ve been a trusted manufacturer of wastewater screening equipment since 1973. Based in the United States, we help clients around the globe, and are known for our innovative solutions.
You can view our full line of products here. If you need help selecting the right wastewater screen, contact us today to speak with one of our ISO-certified specialists.