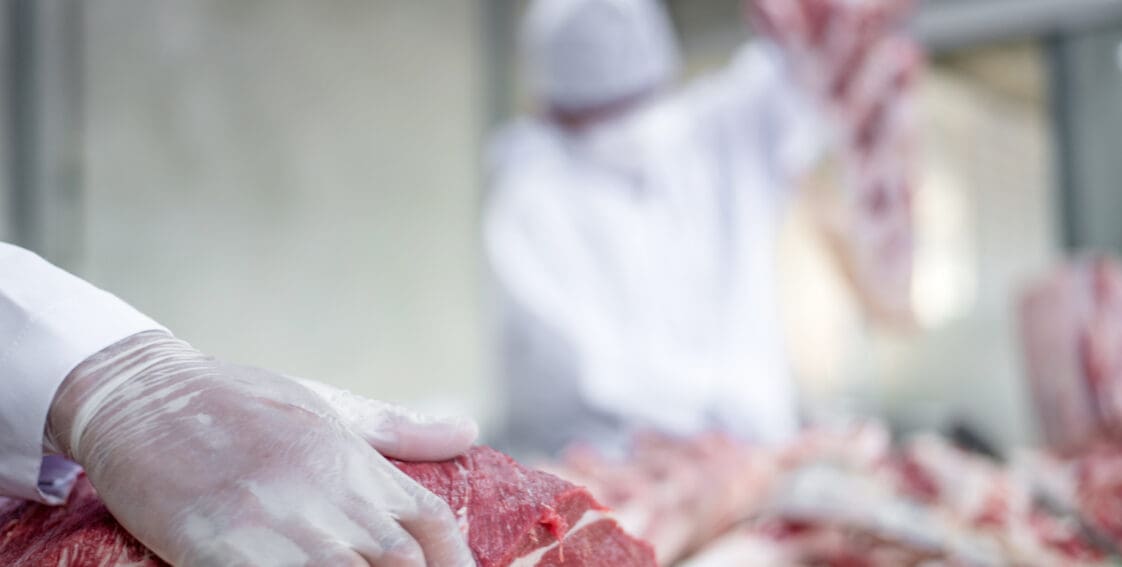
Are You Prepared for the New Meat Wastewater Guidelines?
- How Meat & Poultry Wastewater Affects Public Drinking Water
- Government Meat & Poultry Effluent Regulations
- How to Maintain Compliance
- Customize Your Solution
For the first time in almost two decades, the United States Environmental Protection Agency (EPA) has announced plans to revise its water pollution regulations for slaughterhouses and meat processing plants.
This announcement follows lawsuits from environmental groups claiming wastewater runoff from meat and poultry processing plants has leaked into lakes and streams, polluting the environment and contaminating public water systems.
While the EPA has yet to release its new iteration of the Effluent Guidelines for Meat & Poultry, the agency has announced its intentions to do so by August 2025. This means that meat and poultry processing facilities should begin rethinking their water management processes sooner rather than later.
How Meat & Poultry Wastewater Affects Public Drinking Water
Under current EPA regulations, meat and poultry treatment facilities can release their meat processing wastewater without pretreatment. In fact, according to a 2021 article by The National Provisioner, these facilities “are given the authority to discharge their process wastewater to publicly owned or municipal wastewater treatment works (POTWs) for further treatment,” going on to explain that “the level of pretreatment that occurs at the meat and poultry plants vary and depend on local sewer ordinances or guidelines set by the local municipality.”
The problem with this is that wastewater from these facilities often contains contaminants that can seriously affect public health, including diluted animal blood, fats, and suspended solids. Likewise, there is understandable concern about the effect of these contaminants on wastewater streams. According to the EPA, these wastewater streams have the highest reported phosphorus levels and the second-highest nitrogen levels. Too much phosphorus and nitrogen in water supplies can lead to algae blooms, which can produce toxins that harm the health of humans and wildlife.
Government Meat & Poultry Effluent Regulations
Any business that discharges meat processing wastewater (with or without pretreatment) is affected by the EPA’s existing regulations and will be subject to new regulations as they are announced. If your operation is impacted, you should have received a letter and a questionnaire directly from the EPA with further information.
The existing meat and poultry effluent regulations (originated in 1974) set specific standards and rules for how wastewater can be discharged to surface waters and POTWs nationwide. These regulations were influenced by Title III of the Clean Water Act, which became law in 1972. These guidelines were amended in 2004 but haven’t been revised since then, until now.
The EPA’s current iteration of existing meat and poultry effluent regulations is Program Plan 15, its newest iteration. It is expected that this latest version of the law will state effluent limitations for the following:
- Simple and complex slaughterhouses
- Low- and high-processing packinghouses
- Small processors
- Meat cutters
- Sausage/luncheon meat processors
- Ham processors
- Canned meats processors
- Renderers
- Poultry-first and poultry-further processing
How to Maintain Compliance
If you run any meat processing business, now is the time to start thinking about how you will maintain EPA compliance once these new regulations are implemented.
As previously stated, meat and poultry plants will have until August 2025 to rethink and redefine their waste management processes—and JWC Environmental is here to help.
We offer a selection of products and systems that can help meat processing plants remove process water from solids, protect downstream equipment,
We offer a selection of products and systems, including our IPEC internally or externally fed rotary drum screens and Monster® industrial shredders that can help meat processing plants precondition solids, reduce waste volume, reduce transportation and maintenance costs, and maintain compliance with existing and upcoming regulations.
Drum Screens
We offer internally and externally fed screening technology, which can be fully customized to meet your needs.
Internally Fed
Our IPEC internally fed rotary drum screens (IFO, IFU, and IFS) are ideal for providing superior solids recovery from waste streams, thus reducing the amount of waste discharged from meat and poultry processing operations. Our all-stainless steel drum screens work by rotating at 4 to 5 RPM, allowing liquid to flow out while internal flights drive solids out of the end of the drum. They’re easy to maintain; all that’s needed is to spray it intermittently to keep it clean. The flow rate will vary based on the model—our IFS model offers the highest flow rate capacity (up to 6,500 GPM, depending on the screen design). JWC Environmental offers screen designs for specific applications, like capturing feathers, fats, or meat.
Externally Fed
Our self-cleaning externally fed drum screen is designed to work well in scum applications and in wastewater that has high oil or grease loadings. In our externally fed rotating drum screen, raw influent enters its headbox, distributing wastewater evenly on the external surface of the screen. When wastewater runs through the screen, solids are kept on the outside, rotated to the front of the screen, and removed by a fixed doctor blade. All of the screened solids can be discharged into a dumpster or one of our presses or conveyors. This model is designed to provide 100% overflow protection for flows up to 5 MGD.
Monster Industrial® Shredders
JWC Environmental’s line of Monster Industrial® shredders includes 1-SHRED, 3-SHRED & 3-SHRED-2, 4-SHRED-2, and 7-SHRED-2. All of these shredders are designed to effectively reduce the volume of waste to reduce BOD levels in further waste treatment processes and remove process water from solids. As a result, this meat waste processing equipment is ideal for such applications as slaughter or abattoir, rendering, poultry offal, and animal/pet feed.
Each of our industrial shredders features two rows of sharp, high-torque steel cutters that rotate slowly to reduce challenging solids down to size. The main difference between specific models is the motor’s power, cutting chamber lengths, and throughput range. The smaller 1-SHRED is suited for small applications; it has a standard 3-HP motor with a throughput range of up to 43 ft3/hr. Comparatively, our largest model, the 7-SHRED-2, takes up more space but is ideally suited for difficult size reduction jobs. It has a throughput range of up to 1,504 ft3/hr, depending on the material being processed, and can feature powerful motors up to 100 HP.
All models can come with optional custom hoppers and stands, food-grade, nickel-plated or stainless steel cutting chamber components, customizable cutters, and/or steel scrapers.
HYDRO In-line Series
JWC Environmental’s HYDRO series of grinders, particularly the 1-HYDRO, 3-HYDRO, and 4-HYDRO, are ideal for meat and poultry processing applications. Available as In-line or Open-channel models, these industrial grinders feature dual-shafted, customizable, high-torque cutters that rotate slowly to efficiently reduce the size of challenging solids in industrial sludges and slurries that can damage downstream equipment.
The 1-HYDRO In-line and Open-channel models are ideal for small wastewater applications. The 1-HYDRO In-line model can easily bolt onto existing pipelines (with 4- to 6-inch diameters), features a standard 2 HP motor, and has a flow rate capacity of up to 550 GPM. The Open-channel model is compact without compromising grinder performance, features a standard 2 HP motor and flow rate capacity of up to 180 GPM, and is available with an optional immersible motor and custom guide frames.
The 3-HYDRO In-line model is designed for small to medium applications. It is compact and can be installed into pipelines with 4- to 12-inch diameters. It also has a standard 5 HP motor and a flow rate of up to 2,450 GPM. The 3-HYDRO Open-channel can fit within most wastewater channels and comes with optional custom guide frames, immersible motors, and hardened steel cutters. It has a standard 5 HP motor and flow rates up to 5,620 GPM.
The 4-HYDRO In-line is our most powerful industrial In-line grinder, featuring a standard 10 HP motor and a flow capacity of up to 6,860 GPM. While also featuring a compact design, the 4-HYDRO does have a bigger footprint than the 3-HYDRO, fitting into 12- to 20-inch diameter pipelines. Likewise, the 4-HYDRO Open-channel is our most powerful Open-channel model. It features a standard 10 HP motor and a flow rate capacity of up to 2,100 GPM. The Open-channel model also has a compact design, making it ideal for most wastewater channels, and can come with optional custom guide frames, corrosion-resistant steel cutters, and immersible motors.
Customize Your Solution Today
Since 1973, JWC Environmental has been an industry-leading manufacturer of innovative wastewater equipment and technology. We’re committed to helping our customers solve even the most difficult waste reduction and recycling challenges.
Please contact us today to learn more about our systems or to request a consultation with one of our product specialists.